Serge - Chef de projet ARIBA
Ref : 120726T001-
Domicile
10100 PRAGUE (République Tchèque)
-
Profil
Chef de projet, Consultant (52 ans)
-
StatutFreelance
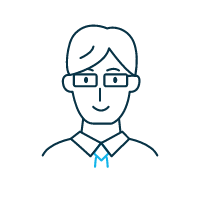
-
Project Management – Prague eCatalogue projects (in France)
AribaJan 2011 - Jan 2012Leading Steel company : Migrating all european catalogues to Ariba Cloud solution, including
enablement of major partners to Ariba Network.
eProcurement projects (in France, US)
- Leading Oil & Gas company : Implementing Procure2Pay Ariba Cloud solution for a major BU -
Digi-Guide – Entrepreneur, iPhone apps development – Paris
Software / Product developmentJan 2004 - Jan 2011- Objective C (iOS platform), Embedded C++, ActionScript
Project Management
- Product development from product definition to Sales with key partners (AVIS, Paris Tourist Office, …)
- Creation of a strong local partner network : Italy, Spain, UK, Russia, Argentina, Germany -
2000 - aujourd'hui
eCatalog implementation
Situation : Major steel manufacturer decided to migrate its eCatalogs from an on-premise tool to
Ariba Cloud solution.
Task : Lead the eCatalog implementation as Project Manager.
Action : Identify business requirements to configure and customize Ariba Cloud software to
client’s needs, implement solution, migrate all catalogs to new format, enroll and train
suppliers on new solution.
Result : We migrated 132 catalogs (representing over 650 000 items), created more than 100
parametric attributes to comply with highly technical item search, enabled over 100
suppliers, rebuilt the catalog hierarchy, created over 300 views. -
PRTM – Consultant (Manager level) – Paris (3 years), Frankfurt (2 years)Jan 1999 - Jan 2003
Supply-Chain projects (in France, Germany, Switzerland, Italy, England, Spain, Poland)
- Main industries : Telecom, FMCG (cosmetics), Automotive, Chemical
- Main tasks : Supply-Chain process design, SC process implementation, SC benchmarking, SC cost reduction, SC Planning redesign, SC service level improvement
NPD - New Products Development projects (in France, Belgium, Italy)
- Main industries : Electronics, Chemical, Ship Building
- Main tasks : Assessing Product Development activities, identifying opportunities for change and designing a target model, Designing and implementing a NPD process after a merger -
Euromold-Alcatel N.V. - Logistic Engineer – Aalst (BE) & Dortmund(DE)Jan 1996 - Jan 1999
- In-House logistics redesign and implementation
- Implementation of an ERP software in 3 different sites (Belgium, France and Germany)
- Purchasing (negotiation, management of European suppliers)
IT Implementation
eCatalog implementation
Situation : Major steel manufacturer decided to migrate its eCatalogs from an on-premise tool to Ariba Cloud solution.
Task : Lead the eCatalog implementation as Project Manager.
Action : Identify business requirements to configure and customize Ariba Cloud software to client’s needs, implement solution, migrate all catalogs to new format, enroll and train suppliers on new solution.
Result : We migrated 132 catalogs (representing over 650 000 items), created more than 100 parametric attributes to comply with highly technical item search, enabled over 100 suppliers, rebuilt the catalog hierarchy, created over 300 views. 2000 users created their
purchase requisition through this tool
eProcurement implementation
Situation : Major Oil & Gas company decided to implement an eProcurement software on one of its BUs. Target was to reduce paper work along Purchase Requisition creation, validation
and submission to Supplier.
Task : I was in charge of this implementation as Project Manager.
Action : Assess Client's requirements, conduct workshops, and configure the solution.
Result : Software implemented on time (previous implementation with the same client extended by over 150%). Official communication from our client to Ariba to thank the project team.
Mobile Application development for leader in Car Rental
Situation : A leader in Car Rental wanted to develop a Mobile Application aimed at tourist visiting the islands of Tahiti/Moorea. The purpose was first to further differentiate its offering and
also to get additional revenue
Task : Development of an iPhone Application able to guide tourist through selected routes thanks to the GPS. The Application would give suggestion on where to stop, what to see, where to eat along the way.
Action : Product definition in collaboration with customer, product development on iOS platform (development in objective C), creation of maps for Tahiti and Moorea, on-site test, release on AppStore
Result : The mobile app is now available through the AppStore, and as a device to rent in client's rental premises (********/)
ERP implementation (Lead for Purchasing/receiving modules)
Situation : Management decided to implement an ERP for all 3 Manufacturing/Finishing sites.
Choice of ERP was Glovia (Fujitsu)
Task : Workstream lead for Purchasing / Receiving modules.
Action : To-Be Process description, To-Be vs As-Is gap analysis, Purchasing/Receiving module implementation in coordination with all other ERP modules, data cleansing, testing, training of employees on all 3 sites
Result : ERP was successfully implemented on all 3 manufacturing sites of the company.
Supply-Chain
Supply-Chain cost reduction for a major Chemical leader
Situation : A major chemical corporation identified its Supply Chain cost as one of its main issue to competitiveness on a price sensitive market.
Task : Identify Supply Chain cost improvement potential.
Action : Conduct benchmark study of Supply Chain, ensure benchmark population is aligned
with client’s specifics (process industry, Make To Stock).
Result : Main source for savings were identified within transport. Following this diagnostic, our client initiated a large project with its transport suppliers to reduce this cost.
Supply-Chain target model development to face Service issues (OFLT, OTD)
Situation : A large automotive manufacturer, leader on its market was facing issues related to customer service (Order Fulfilment Lead Time, On Time Delivery).
Task : Define target Supply Chain model to comply with aggressive performance target
Action : Conduct a benchmark study on performance, lead interviews, conduct workshops.
Result : Main findings and recommendations were related to poor planning process leading to wrong items being produced (hence, high stock levels and missed sales). Following this
diagnostic, a new project was launch to select and implement an APS (advanced planning System), Manugistic.
Supply-Chain target model development and implementation in Telecom
Situation : After several large acquisitions, a major leader in Telecom (Carrier business) identified major discrepancies in its Supply-Chain : internal Business Units were working in a Buyer-Supplier relationship, hence increasing OFLT from a final customer’s perspective, and increasing the total Supply Chain cost.
Task : Propose a target Chain model to Streamline the Supply chain at a European level.
Action : Define target model, validate with major stakeholders, pilot this model on smaller BUs.
Result : Target model created and validated by Management. Streamlined order intake on pilot BUs.
Supply-Chain target model development and implementation in FMCG
Situation : European Management of a major FMCG decided to re-engineer its Supply-Chain to cope with current challenges of today's changing market.
Task : 4 workstreams were identified : Sourcing, Manufacturing, Delivery, Planning. I was in charge of leading the Planning Workstream
Action : Measure current performance, define performance goals based on Business targets,
Mapping of the As-Is planning processes, define To-Be in coordination with other
workstreams and pilot this process of some product lines..
Result : Stabilization of planning processes through implementation of weekly demand-Supply balancing meeting
Kanban implementation
Situation : A-type commodities represented both major storage space and time-consuming activity
for Material Planners.
Task : I suggested to implement Kanban for 2 major Commodities : cardboard box and rubber
Action : Define Kanban level, define process in coordination with suppliers, renegociate item
prices (decrease or stable), train employees (own people + supplier’s) on new process
define, pilot, roll-out.
Result : Prices for Cardboard boxes decreased due to renegotiation of batch sizes, both Rubber and Cardboard boxes were removed from MRP calculation (hence more time for planners to focus on other commodities), 10% of storage space freed
Supplier negotiation
Situation : The supplier of a key component refused to decrease its price despite stable design and
stable volume over last 4 years.
Task : Decrease the price of this item (either by negotiation or changing supplier)
Action : Visit this supplier, perform a cost roll-up estimation (based on machine and labor work
along the production process), identify alternatives to this supplier.
Result : As it would have been too expensive to qualify a new supplier for this key component, I
preferred to negotiate with our existing supplier. After negotiation, the supplier agreed to
decrease its price by over 5%, representing 25000€ per year
Management of Innovation / New Product Development
NDP process development and piloting after a large merger
Situation : After 2 major companies in connectors/electronics merged, the new CTO identified that
the differences processes used in New Product Development by both companies were
limiting potential synergies and integration of R&D departments
Task : Develop a new NPD process taking into account best practices from both companies,
with input coming from major european R&D sites and all departments involved in New Product Development.
Pilot this new process on key project to assess efficiency
Action : I spent 4 months with a core team from different departments and different countries,
developing a To-Be NPD process. In the meantime, R&D managers were trained on how to conduct phase reviews.
Once created, I piloted, in close collaboration with project team leaders 2 projects using the new process defined.
Result : On the 2 project I piloted, NPD cycle time was reduced by over 25 %. The NPD process was rolled out to the whole corporation after our consulting team left.
Diagnostic on Innovation activities for a leader in chemicals
Situation : A major Business Unit of a leader in Chemicals identified that their development cycle
time was not under control, leading to missed opportunities, lost clients and low R&D effectiveness.
Task : My firm has been hired to conduct a thorough diagnostic of innovation activities identify the root cause and propose a target model for R&D
Action : I conducted over 20 interviews, followed project review meetings, compiled all figures related to Innovation. All results were benchmarked using PRTM's data. I developed a model able to estimate project duration based on a complexity matrix.
Result : Main findings and recommendations were : the uncontrolled project screening process led to overloaded project pipeline, Development cycle had 30 to 50% decrease potential
compared to benchmark population, Decision-making was siloed and lacked structure and efficiency. A target model has been proposed
Product development redesign in ship building industry
Situation : A major Ship Building company identified several cases where lack of coordination
between departments cost rework and additional delay (causing high penalties).
Task : Identify flaws of the ship development processes.
Action : Conduct interviews, map As-Is process, map sample projects, define target model.
Result : Main findings and recommendations were : as the company let many key employees leave for early retirement without making sure their knowledge was properly documented, a significant part of the company's know-how disappeared. We built a new
structure of a development process, focusing on coordination points between departments
R&D strategy and organization model for a Cash Machine manufacturer
Situation : A recently acquired BU from a large corporation was suffering from uncontrolled development cycle time, lack of R&D strategy to comply with business objectives, and R&D resources misaligned with development requirements.
Task : Provide diagnostic on R&D operations and define target model in line with companywide business objectives.
Action : Gather all figures related to R&D, perform project mapping, conduct interviews, follow PRTM’s methodology to define R&D target model and propose target R&D organization.
Result : We recommended a new approach towards BUY vs MAKE strategy on all major components. A new R&D strategy and its organization was proposed to emphasis the need on integration skills more than individual component expertise -
aujourd'hui
users created their
purchase requisition through this tool
eProcurement implementation
Situation : Major Oil & Gas company decided to implement an eProcurement software on one of its
BUs. Target was to reduce paper work along Purchase Requisition creation, validation
and submission to Supplier.
Task : I was in charge of this implementation as Project Manager.
Action : Assess Client's requirements, conduct workshops, and configure the solution.
Result : Software implemented on time (previous implementation with the same client extended
by over 150%). Official communication from our client to Ariba to thank the project team.
Mobile Application development for leader in Car Rental
Situation : A leader in Car Rental wanted to develop a Mobile Application aimed at tourist visiting
the islands of Tahiti/Moorea. The purpose was first to further differentiate its offering and
also to get additional revenue
Task : Development of an iPhone Application able to guide tourist through selected routes
thanks to the GPS. The Application would give suggestion on where to stop, what to
see, where to eat along the way.
Action : Product definition in collaboration with customer, product development on iOS platform
(development in objective C), creation of maps for Tahiti and Moorea, on-site test,
release on AppStore
Result : The mobile app is now available through the AppStore, and as a device to rent in
client's rental premises (********/)
ERP implementation (Lead for Purchasing/receiving modules)
Situation : Management decided to implement an ERP for all 3 Manufacturing/Finishing sites.
Choice of ERP was Glovia (Fujitsu)
Task : Workstream lead for Purchasing / Receiving modules.
Action : To-Be Process description, To-Be vs As-Is gap analysis, Purchasing/Receiving module
implementation in coordination with all other ERP modules, data cleansing, testing,
training of employees on all 3 sites
Result : ERP was successfully implemented on all 3 manufacturing sites of the company.
Supply-Chain
Supply-Chain cost reduction for a major Chemical leader
Situation : A major chemical corporation identified its Supply Chain cost as one of its main issue to
competitiveness on a price sensitive market.
Task : Identify Supply Chain cost improvement potential.
Action : Conduct benchmark study of Supply Chain, ensure benchmark population is aligned
with client’s specifics (process industry, Make To Stock).
Result : Main source for savings were identified within transport. Following this diagnostic, our
client initiated a large project with its transport suppliers to reduce this cost.
Formation
IT Skills
Expert in : Objective C, Ariba P2P
Working knowledge : ERP (Glovia, SAP), APS (Manugistic)
Education and certification
1999-2003: SCOR trainer to PRTM clients, APICS Certified, 6-Sigma methodology
1995-1996: HEC Paris, Ranked #1 Business School for Executive Education in 2011 by Financial Times
Master in Supply Chain, obtained with honours.
1992-1995: Chemical Engineer :
- Imperial College (London), 4th year Master of Engineering, distinction 2.1
- E.N.S.G.T.I. (Ecole Nationale Supérieure en Génie des Technologies Industrielles) in Pau (France).
Langues :
French : Mother tongue.
English : fluent. 1 year in London (1994-95), many projects in England.
German : fluent. 2 year in Germany (2002-2003), many projects in Germany.
Spanish : fluent. Many projects in Spain.
Dutch : advanced beginner. 2 years in Flanders
Czech : advanced beginner. Married to a Czech wife, based in Czech Republic (Prague)
Formation
IT Skills
Expert in : Objective C, Ariba P2P
Working knowledge : ERP (Glovia, SAP), APS (Manugistic)
Education and certification
1999-2003: SCOR trainer to PRTM clients, APICS Certified, 6-Sigma methodology
1995-1996: HEC Paris, Ranked #1 Business School for Executive Education in 2011 by Financial Times
Master in Supply Chain, obtained with honours.
1992-1995: Chemical Engineer :
- Imperial College (London), 4th year Master of Engineering, distinction 2.1
- E.N.S.G.T.I. (Ecole Nationale Supérieure en Génie des Technologies Industrielles) in Pau (France).
Langues :
French : Mother tongue.
English : fluent. 1 year in London (1994-95), many projects in England.
German : fluent. 2 year in Germany (2002-2003), many projects in Germany.
Spanish : fluent. Many projects in Spain.
Dutch : advanced beginner. 2 years in Flanders
Czech : advanced beginner. Married to a Czech wife, based in Czech Republic (Prague)